CNC Machining Part Factories: Revolutionizing Metal Fabrication
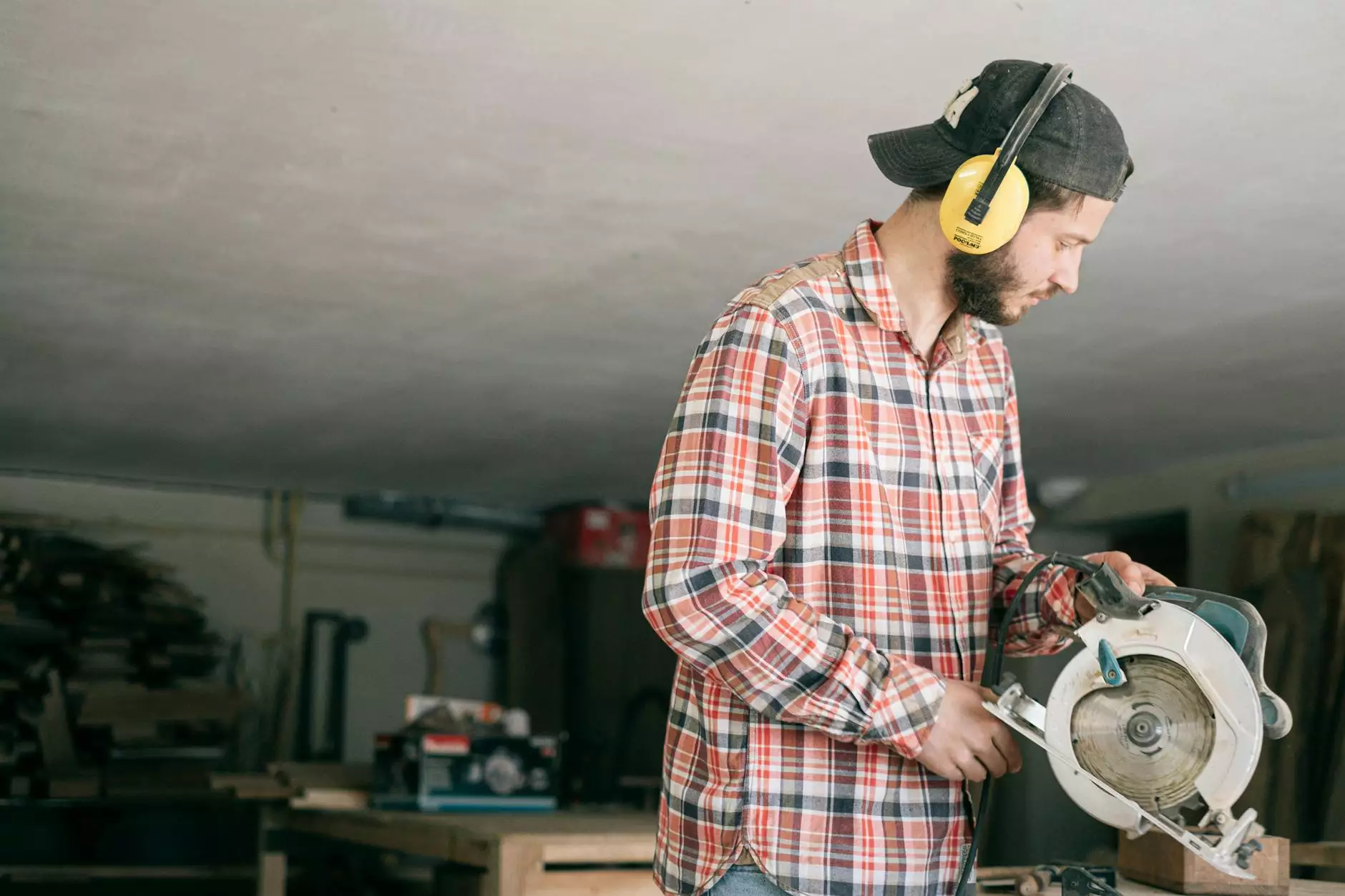
CNC machining part factories are at the forefront of modern manufacturing, delivering precision-engineered components that drive the functionality of various industries. From aerospace to automotive, the demand for high-quality parts manufactured with utmost accuracy is crucial. This article explores the workings of CNC machining part factories, their benefits, and their contribution to innovation in metal fabrication.
The Importance of CNC Machining in Modern Manufacturing
Computer Numerical Control (CNC) machining is a subtractive manufacturing process that involves the use of pre-programmed computer software to control the movement of factory tools and machinery. The significance of this technology lies in its ability to produce extremely precise parts at scale, which is essential in industries where tolerances are tight, and performance is critical.
Key Advantages of CNC Machining
- Precision and Accuracy: CNC machines can achieve tolerances as tight as ±0.001 inches, which ensures that parts fit perfectly in their intended applications.
- Consistency: Once a design is programmed, CNC machines can produce thousands of identical parts without variation, maintaining high quality throughout the production run.
- Complex Designs: CNC machining allows for the creation of intricate geometries and features that would be challenging or impossible to achieve with traditional machining methods.
- Cost-Effectiveness: While the initial investment in CNC machinery can be significant, the reduction in labor costs and increased production speed often lead to lower per-piece costs.
- Material Versatility: CNC machining can work with a broad range of materials, including metals like aluminum, steel, and titanium, as well as plastics and composites.
How CNC Machining Part Factories Operate
CNC machining part factories employ a systematic approach to manufacturing that begins with precise design and ends with quality assurance. Below, we outline the essential steps involved in the CNC machining process:
1. Design and Prototyping
The process starts with a detailed design that engineers create using CAD (Computer-Aided Design) software. This design is translated into a G-code instruction set that directs the CNC machine on how to cut, mill, and shape the material. Prototyping may occur to validate the design before full-scale production.
2. Material Selection
Choosing the right material is vital for the functionality of the part being manufactured. Factors influencing this choice include the part's intended use, the environment it will operate in, and cost considerations. Common materials used in CNC machining part factories include:
- Aluminum
- Stainless Steel
- Brass
- Carbon Steel
- Plastics (e.g., Nylon, Delrin)
3. Setup and Machining
Once the material is selected, CNC operators prepare the machinery for production. This involves securing the workpiece and calibrating the machine according to the specifications of the G-code. The machining process itself can involve various operations, including:
- Milling: Cutting away material from a solid block to create the desired shape.
- Turning: Rotating the workpiece against a fixed cutting tool to create cylindrical parts.
- Drilling: Creating holes of specific diameters in the material.
- Electrical Discharge Machining (EDM): Using electrical sparks to erode material in intricate shapes.
4. Finishing and Quality Control
After machining, parts often require finishing processes such as sanding, polishing, or coating to meet surface finish requirements. Quality control is critical in this stage; rigorous testing confirms that every part meets design specifications and tolerances. Methods of quality assurance include:
- Dimensional Inspection: Using calipers and gauges to measure dimensions accurately.
- Visual Inspection: Checking for surface defects or inconsistencies.
- Functional Testing: Testing parts in real-world conditions to ensure they perform their intended function.
Applications of CNC Machined Parts
Due to their versatility and precision, parts produced in cnc machining part factories find applications across numerous fields:
Aerospace Industry
The aerospace sector relies heavily on CNC machined components because they require rigorous safety and quality standards. Parts such as engine mountings, brackets, and housings are custom machined to meet stringent specifications.
Automotive Manufacturing
In automotive production, CNC machining plays a crucial role in creating components that contribute to vehicle performance and safety. Examples include engine blocks, transmission housings, and custom components for electric vehicles.
Medical Equipment
The medical field demands high-precision components for devices such as surgical instruments, prosthetics, and diagnostic equipment. CNC machining meets these demands through its ability to produce complex shapes and high-tolerance parts.
Consumer Electronics
From the frames of smartphones to intricate circuit boards, the consumer electronics industry benefits from the precision of CNC machining. Parts are often produced in short runs to adapt quickly to market changes without disruptions.
Choosing the Right CNC Machining Part Factory
With numerous CNC machining part factories globally, selecting the right partner for your manufacturing needs is critical. Consider the following factors:
1. Experience and Expertise
Look for factories with a proven track record in your industry. An experienced factory will better understand your specific requirements, including materials, design challenges, and production techniques.
2. Technology Capabilities
Modern CNC machining utilizes advanced tools and software. Ensure that the factory employs up-to-date technology, including multi-axis machines, automated systems, and high-quality CAD/CAM software for design optimization.
3. Quality Certifications
Verify that the factory holds relevant quality management certifications such as ISO 9001. This certification signifies a commitment to quality control and continuous improvement.
4. Customer Support
Effective communication and support can make a significant difference in the manufacturing process. Look for factories that prioritize client relationships and are willing to provide updates on production status, timelines, and any potential issues.
The Future of CNC Machining Part Factories
The future of cnc machining part factories appears bright, with ongoing advancements in technology and manufacturing processes. The following trends are shaping the evolution of CNC machining:
1. Integration of Industry 4.0
The rise of Industry 4.0 is bringing automation and data exchange into manufacturing, allowing for smarter factories. CNC machines will become more connected, facilitating real-time monitoring, predictive maintenance, and enhanced production efficiency.
2. Additive Manufacturing Technologies
Many CNC machining part factories are exploring the integration of additive manufacturing (3D printing) to create hybrid machining processes. This combination will enable faster prototyping and the production of complex geometries that traditional methods cannot achieve alone.
3. Sustainability Initiatives
As environmental concerns grow, CNC machining factories are focusing on sustainable practices. This includes reducing waste through optimized cutting processes, recycling materials, and utilizing energy-efficient machinery.
4. Enhanced Training Programs
As technology evolves, so must the workforce. Factories are investing in comprehensive training programs to ensure that employees are well-versed in modern techniques, software, and machinery to maintain competitive advantages.
Conclusion
In conclusion, cnc machining part factories are essential players in the metal fabrication industry, exemplifying precision, efficiency, and adaptability. The ability to create complex, high-tolerance components for various applications underscores their significance in driving technological advancement across multiple sectors. As these factories continue to evolve with technology and market demands, they will remain at the core of innovation in manufacturing.
For businesses looking to leverage CNC machining, partnering with a reputable factory like DeepMould.net can lead you toward achieving your production goals with the highest standards of quality and efficiency. Embrace the future of machining, and experience the benefits of advanced manufacturing.